Textile Technology
Our prime capability is textiles. We are one of the few companies in the world with expertise in the use of embroidery for technical applications such as surgical implants or automotive and aerospace. We also have specialist knowledge of weaving, braiding and knitting technologies, and their application for industrial uses.
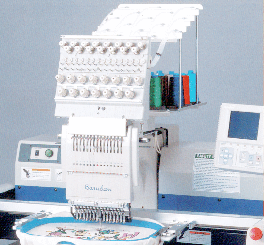
Embroidery machinery, such as illustrated here, is computer controlled, high output machinery, ideal for both surgical implant manufacture and for the production of preforms for composite manufacture (reinforced plastics).
Embroidery
Through Stitching
Elastic Narrow
Fabrics
Composites
Engineering Textiles
Embroidery
What is Embroidery for Technical Textiles?
Embroidery is defined as work with needle and thread upon cloth. Commercially today most embroidery is made using a computer controlled machine to move the cloth around below a sewing head. The method of stitching on most embroidery machines is a lockstitch, which is the type of stitch produced by most domestic sewing machines, and uses a similar needle action, and the same type of bobbin found on domestic machines. The main difference is the addition of many more sewing needles (which can be changed automatically, usually to change colours), and the movement for the embroidery frame.
Designs are produced quickly and easily on a computer, with special software, and then the design can be given to the machine on a standard computer disk. Once the embroidery machine is threaded up, the frame filled with the right cloth, the button can be pressed and the whole embroidery produced automatically.
In collaboration with Ellis Developments, Rae Developments have taken these well established techniques, but applied them to technical problems such as the need to strengthen glass fibre reinforced floors for automobiles in specific places where the highest strength is needed, such as the seat belt anchorages, which become highly loaded during an accident. Making the whole floor of the car very strong is another solution, but the extra weight adds to the running costs of the car for its whole life: the use of a glass washer, with all the fibres within it placed in such a way that the high loads are distributed away from the anchor hole in the most efficient way, is the most cost effective solution.
The development of this and other products made in the same way was developed during a major research project, called the MASCET project. Currently we are involved in the development of a number of experimental components for an aircraft wing using carbon fibre in order to reduce the weight of the wing. The carbon is laid down using one or other embroidery techniques to optimise the fibre architecture and hence the structural efficiency of the component. This leads to reduced weight, and thus fuel saving.
Back to top
Through Stitching
Through Stitching of Composites
Ellis Developments have developed a number of techniques for through stitching composites to reduce delamination. This includes both dry fibre lay-ups and prepreg. We believe that we are the only company capable of through stitching pre-impregnated fabrics, and particularly have demonstrated corner reinforcement, corners being particularly susceptible to delamination. Products normally show considerably improved impact resistance.
Through stitching can be done on fairly large areas of flat dry reinforcement quite quickly and easily using conventional embroidery machinery, but pre-impregnated fabrics (pre-pregs) are more difficult, and need our special techniques developed in-house.
We can through stitch with polyester, glass, aramid and PBO, and are examining other fibres. Carbon is currently very difficult, because it is so stiff and is currently only available in relatively large thicknesses unsuitable for sewing.
We will be pleased to look at your particular problem, we may well be able to help. Do contact us to begin a discussion.
Back to top
Elastic Narrow Fabrics

Back to top
Composites
We are in the forefront of technical developments in the manufacture of stitching technology for preforms for composites.
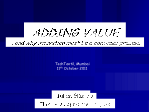
Click on image above to download presentation Tech Textile Asia Conference (India).
Structural Health Monitoring
We are in the forefront of technical developments in the manufacture of stitching technology for preforms for composites.
We have developed a method for incorporating sensors for the continuous electrical measurement of load and impact events on composites (including carbon) for structural health monitoring (SHM).
A small bridge was manufactured to demonstrate the way of using this technology.
We envisage applications such as composite fuselages, yacht masts, sails, deep sea structures, oil installations, racing cars, bridges, to name but a few.
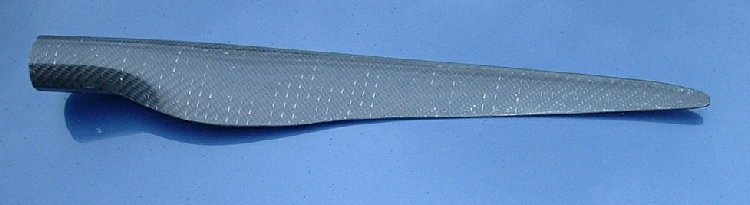
model wind turbine blade incorporating the sensors
Back to top
Embroidered Textile Preforms
The MASCET project was a major project to look at embroidered textile preforms for composites. There are ongoing developments of this technology in progress. Their major advantages include efficient structural architecture (meaning light weight) and very low waste levels during manufacture.
Click on image to open a PDF version of the MASCET final project report.
Back to top
Through Stitching
The ZARC project, for Z-axis reinforcement studied through stitching using computerised equipment to place the stitches exactly where required. This work is continuing, but some of it is of a commercially sensitive nature, and covered by confidentiality agreements, so cannot be described here. We will be pleased to hear from you with enquiries, however, where we can update you as to progress. We are now exploiting our work on through-stitching carbon prepreg, and can carry out work to reduce delamination on composites.
We are currently carrying out work on through stitching pre-impregnated carbon fibre for composites. This has long been considered almost impossible, but we are achieving exciting results on 6 mm thick lay-ups, and usually use PBO as a through stitching material, which has better moisture relations than Kevlar, although are currently examining other materials. We have also been successful with Kevlar and glass. For further details contact us.
Through-Thickness Reinforcement of Composites for Improved Impact Resistance and Delamination Resistance
Through Stitching)
The Mascet project studied the potential for the use of embroidery in the manufacture of structural composites (reinforced plastics) and was completed in 1997. Since then Ellis Developments have examined the use of stitching technologies to hold together different layers of textiles, similarly for use in structural composites.
Through thickness stitching has the potential to reduce the splitting apart of the layers, which are used to form many textile reinforced composites. If the finished part is subjected to a heavy impact, there is a danger that the layers may delaminate, and the composite will fail in its task. Through stitching has been found to improve impact resistance, and may have particular application in aircraft which are subject to bird strikes.
The ZARC Project was an initial study part funded by the European Community’s Framework research fund, and was run in collaboration with Teritex and the University of Nottingham, Department of Mechanical Engineering. The results of the literature study indicated that there is considerable confusion about what can be achieved: we believe we can bring some considerable clarity to the subject through our knowledge of the subject.
Our work on through stitching is continuing at Ellis Developments in conjunction with QinetiQ at Farnborough, England, Airbus UK and others. Through stitching is proving to be a rapid, flexible and inexpensive method of achieving the desired results.
The reinforcement of corners is usually possible, and we have successfully through-stitched prepregs (fabrics pre-impregnated with resin), and have developed this and can provide a service to customers. The through stitching demonstrates significantly improved impact resistance characteristics.
Back to top
Node and Truss Structures
The NOTS project (Nodal Optimisation of Truss Structures), looked at node and truss structures. This work re-examined the work done by Barnes Wallace for the Wellington Bomber programme in the Second World War, and considers applications on modern aircraft using modern raw materials and techniques.
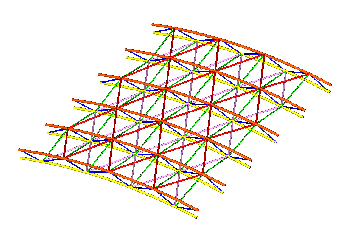
Project Overview
The overall aim of the project was to establish the underpinning science and technological know-how concerning the use of novel lightweight composite nodal truss structures in aerospace and other sectors. The project developed the enabling know-how and innovation in joints and joining for the manufacture of truss test structures by providing:
- Improved performance and structural integrity with emphasis on weight reduction
- Increased service life thereby reducing life cycle costs
- Adhesive bonding technologies for joining lightweight composites
- Joining technologies for repair e.g. low temperature cure minimising residual stresses
- 3D theoretical modelling and validation of nodal joints and structures under realistic loads and environments.
Truss structures inherently provide highly distributed stress paths that can be utilised to provide outstanding damage tolerance performance, with failure contrived to occur by serial failure of struts. Critical to the successful development and implementation of advanced truss structures are software tools that assist in the structural design and performance analysis, coupled with cost-effective manufacture and repair. Previous investigations of truss structures required tedious experimentation for each node, and the development of suitable modelling tools in this project for both design and performance (including the effects of damage and damage tolerance) form a major and critical part of the work. Ease of repair is also important in life cycle costs. Generic know-how and design/performance tools were generated.
This collaborative project had a value of £700,000, and was part-funded by The UK’s Department of Trade and Industry.
Back to top
Engineering Textiles
Most of our engineering textiles are based in composites, described elsewhere. However, we are always interested to develop new textile based products using the wide range of techniques available to us. Much of our work is commercially sensitive.
We have specialist knowledge of load bearing textile technology, and have applied much of this to our work in orthopaedics and aerospace and automotive textiles. If you have any requirements, please contact us for a discussion without obligation. We have recently developed through stitching techniques for textiles for composite, which have pre-impregnated with resin (prepregs).
Another example of specialist textiles is our development of novel technology using embroidery for the manufacture of loudspeaker cones. This technology is covered by granted patents.
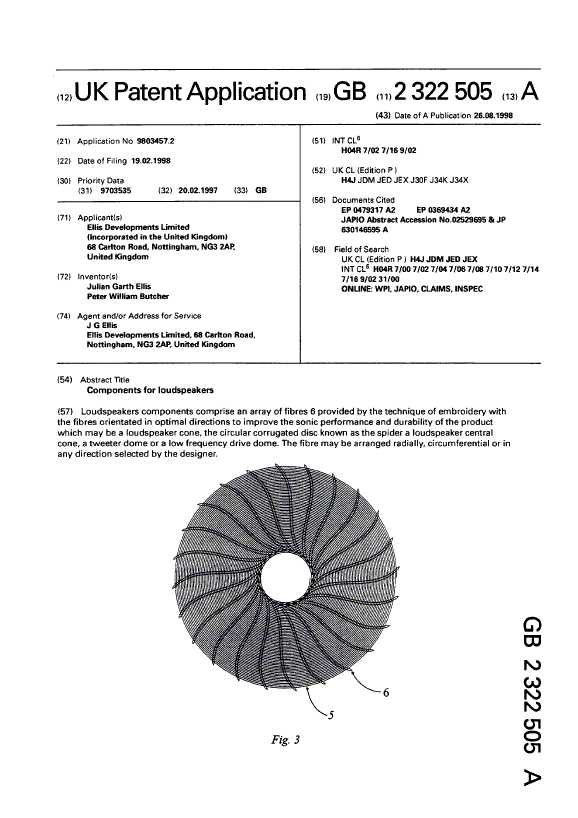
Back to top
Address
1, Fair A Far, Cramond
Edinburgh,
Scotland
EH46QB
Contact Us
(+44) 07759248863
michelle@raedevelopments.com